What is the troubleshooting process for abnormal vibration of coaxial TY100-28-2.2KW reducer
The troubleshooting process for abnormal vibration of coaxial TY100-28-2.2KW reducer can be carried out according to the following steps:
1. Observation record:
Observe the timing, frequency, and amplitude of vibration, record operating conditions such as load, speed, temperature, etc., in order to provide a basis for subsequent analysis.
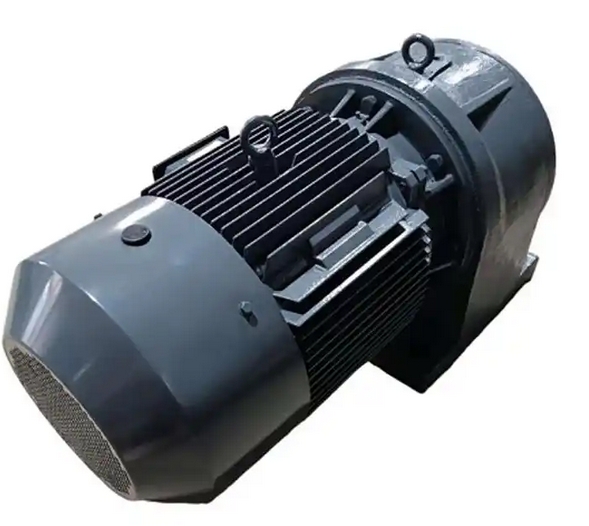
2. Check the installation status:
Check if the installation foundation of the reducer is firm and if the anchor bolts are loose. Use a wrench to tighten the bolts to ensure a reliable connection.
Use a spirit level to check if the installation plane of the reducer is level. If it is not level, it needs to be adjusted to ensure that it is in a horizontal state.
3. Troubleshooting transmission components:
Check for wear, cracks, or foreign objects embedded in transmission components such as gears, bearings, and couplings. If the gear is severely worn, it will cause poor meshing and needs to be replaced in a timely manner; Bearing damage, such as ball wear, track scratches, etc., can also cause vibration and should be replaced.
Check whether the rotating components such as impellers and shafts are balanced. Unbalanced rotating components may cause vibration. If there is a problem, perform dynamic balance correction or replace the components.
4. Check the lubrication system:
Check if the oil level of the gear oil is normal. If the oil level is too low, add lubricating oil that meets the requirements.
Check the quality of the oil, observe whether the oil has deteriorated or been contaminated. If the oil does not meet the requirements, it should be replaced in a timely manner, and a filter or filtering device should be added to the oil circulation system. Regularly clean and replace the filter element.
Confirm whether the type and specifications of the lubricating oil meet the requirements for the use of the gearbox. Improper lubricating oil may lead to poor lubrication effect, and suitable lubricating oil should be selected.
5. Check the electrical part:
Measure whether the power supply voltage and frequency are stable, whether the phase is correct, and ensure that the power supply is normal.
Check whether the wiring of the motor and reducer is firm and whether the insulation is good. If there is any looseness or insulation problem, it should be repaired in a timely manner.
6. Fault analysis:
If conditions permit, vibration analysis instruments can be used to analyze the vibration of the gearbox, identify the frequency components of the vibration, and combine previous observations and inspection results to determine the source and specific cause of the vibration.
7. Problem solving:
Take corresponding maintenance measures based on the identified causes. Replace worn or damaged gears, bearings, and other components; Adjust the installation position again to ensure the coaxiality between the reducer and the motor; Tighten loose bolts, etc.
If the problem is caused by design or manufacturing defects, the gearbox manufacturer should be contacted in a timely manner to seek a solution.
8. Operation review: After completing the maintenance, start the gearbox, observe its operating status, check if the vibration has been eliminated, and pay attention to other issues such as abnormal noise and high oil temperature to ensure that the gearbox returns to normal operation.