What are the differences in daily maintenance between gear reducers and worm gear reducers?
Due to their different structures and working principles, gear reducers and worm gear reducers have some differences in daily maintenance, mainly reflected in the following aspects:
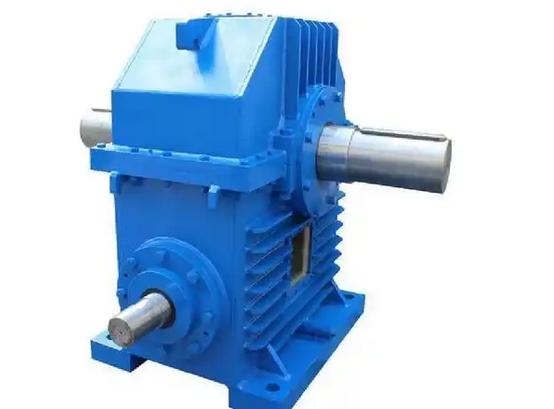
lubrication system
gear reducer
Usually, medium load industrial gear oil is used for lubrication, and the appropriate viscosity grade is selected according to different working conditions and requirements.
Oil level inspection is relatively convenient, and generally the oil level gauge can be used to directly observe whether the oil level is within the normal range.
Due to the high efficiency of gear transmission, the heat generated is relatively low, and the replacement cycle of lubricating oil is relatively long, usually every 5000-10000 hours of operation or at least once a year.
worm gear reducer
Generally, special oil for worm gear and worm gear is used, which has good anti adhesive and lubricating properties, and can meet the special requirements of worm gear and worm gear transmission.
The oil level check may vary depending on the structure of the gearbox, and some require specific oil plug holes to check the oil level.
Worm gear transmission has low efficiency, high heat generation, and lubricating oil is prone to deterioration, so the replacement cycle is relatively short. Usually, the oil quality needs to be checked every 2000-3000 hours of operation, and the lubricating oil should be replaced in a timely manner according to the situation.
Heat dissipation requirements
Gear reducer: The gear transmission efficiency is high, and the heat generation is relatively low. Generally, natural heat dissipation can meet the requirements. In situations where the ambient temperature is high or the load is heavy, it may be necessary to add auxiliary cooling devices such as cooling fans.
Worm gear reducer: Due to low efficiency and high heat generation, it requires high heat dissipation. In addition to ensuring sufficient ventilation space around the gearbox, it may also be necessary to use forced air cooling, water cooling, and other heat dissipation methods to prevent excessive oil temperature from causing a decrease in lubrication performance and component damage.
Wear inspection
gear reducer
The wear of gears is mainly concentrated on the tooth surface, and the wear condition can be checked by observing the wear marks on the tooth surface and measuring the tooth thickness.
Due to the relatively simple shape and structure of gears, inspection is more convenient, and tools such as calipers and tooth thickness gauges can be used for measurement.
worm gear reducer
The wear of worm gears and worm gears is quite complex, not only the tooth surface will wear, but also the spiral part of the worm gear and the hub of the worm gear may experience wear.
During inspection, specialized measuring tools and instruments such as coordinate measuring instruments are required to measure various parameters of the worm gear and worm to determine the degree of wear. At the same time, it is also necessary to pay attention to checking the meshing between the worm gear and worm gear, whether there are problems such as unbalanced load and poor contact.
Installation and alignment requirements
Gear reducer: requires relatively low installation accuracy and alignment, allowing for a certain degree of installation error. However, during installation, it is still necessary to ensure that the connection between the reducer, motor, and working machine is firm to avoid vibration and noise caused by looseness.
Worm gear reducer: requires high installation accuracy and alignment. During installation, it is necessary to strictly follow the requirements for alignment and adjustment to ensure that the axis of the worm gear and worm gear are perpendicular to each other and the center distance meets the requirements. Otherwise, it will lead to poor meshing of the worm gear, exacerbate wear, reduce transmission efficiency, and even cause equipment failure.