What could be the reasons for abnormal vibrations during the trial operation of a large gear reducer after maintenance?
The main reasons for abnormal vibration during the trial operation of large hard tooth surface reducers after maintenance are as follows:
Gear problem
Abnormal meshing: When there is pitting, peeling or tooth profile error on the contact surface of the gear pair, the contact area of the tooth surface will shift, resulting in periodic impact loads and vibration. In addition, gear eccentricity (radial runout>0.05mm), axis parallelism exceeding tolerance (>0.02mm/m), or improper meshing clearance (standard clearance 0.1-0.3mm, after wear>0.5mm) can also cause vibration.
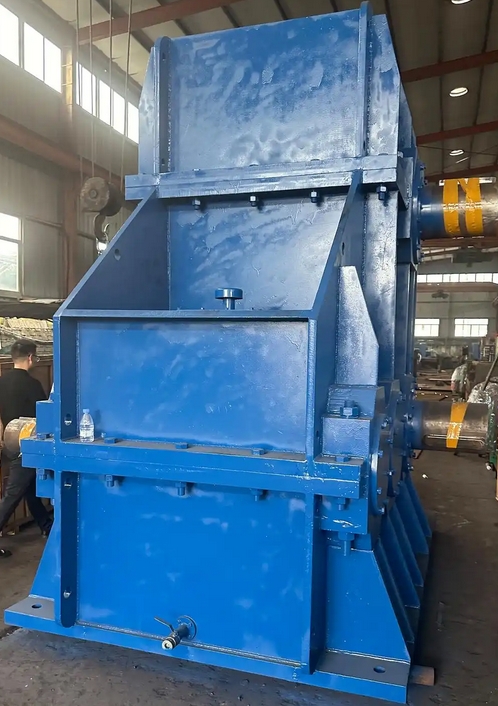
Wear or damage: Gear tooth surfaces may experience wear due to metal particles, dust, or poor lubrication, resulting in thinning of tooth thickness, deformation of tooth profile, and increased backlash. This can increase the dynamic load on the gear, leading to vibration. In addition, gear breakage and other damages can also cause abnormal vibrations.
Insufficient machining accuracy: If the machining accuracy of the gear is insufficient, the tooth profile surface will not be smooth, and collisions and vibrations will occur during operation.
Bearing issues
Damage: The rolling elements, raceways, retainers, and other components of the bearing are damaged by wear, cracks, peeling, and breakage, which can cause unstable rotation and vibration.
Improper installation: When installing bearings, if the installation clearance is too large or too small, or if the bearings are installed askew, it will cause uneven force on the bearings during operation, resulting in vibration. For example, improper adjustment of the axial preload force of tapered roller bearings can cause excessive preload force to raise the bearing temperature, leading to lubrication failure and subsequent vibration.
Bearing seat wear: Bearing seat wear can cause excessive clearance between the bearing seat and the outer ring of the bearing, thereby exacerbating vibration.
Installation and alignment issues
Uneven foundation installation or loose anchor bolts: Uneven foundation installation (levelness>0.1mm/m) or loose anchor bolts of the gearbox can cause the gearbox to shake during operation, resulting in vibration.
Poor shaft alignment: Poor shaft alignment between the reducer and the drive motor or other equipment. When the parallel deviation exceeds 0.05mm/m, the vibration intensity will increase by 3-5 times. Flexible couplings cannot fully compensate for deviations, and may instead generate periodic bending moments due to angular deviations, causing vibration.