Maintenance and care methods for the NCD400-112-1 planetary gear reducer
The following are the maintenance methods for the third level NCD400-112-1 planetary gear reducer:
Daily maintenance
Check lubrication condition: Regularly check the oil level to ensure it is within the normal range. If the oil level is found to be too low, promptly replenish N120 # industrial gear oil of the same model. At the same time, observe the oil quality. If the oil deteriorates, emulsifies, or contains impurities, it should be replaced in a timely manner. Following the manufacturer's recommended oil change cycle, the first oil change should generally be performed after 200-300 hours of operation. For gearboxes that have been continuously operated for a long time, new oil should be replaced after 5000 hours of operation or once a year. For gearboxes that have been out of service for a long time, new oil should also be replaced before resuming operation.
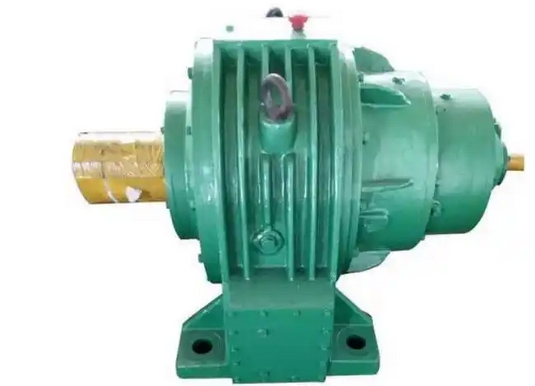
Maintain equipment cleanliness: Regularly clean the surrounding environment of the gearbox, remove dust, dirt, and debris from the surface, and prevent them from entering the interior of the gearbox. At the same time, keep the area around the equipment clean and avoid the accumulation of debris.
Check fasteners: Regularly inspect the fasteners of various parts of the gearbox, such as bolts, nuts, etc., to ensure that they are firmly connected and free of looseness. If there is any looseness, it should be tightened in a timely manner.
regular inspection
Seal inspection: Regularly inspect the seals and sealing devices of the gearbox, such as oil seals, sealing rings, etc., to ensure no leakage. If damaged or poorly sealed seals are found, they should be replaced in a timely manner.
Vibration and noise inspection: Monitor the sound of the gearbox during operation and observe its vibration situation. If there is abnormal noise or vibration, it may be caused by internal component wear, looseness, or other faults. It is necessary to stop the machine in a timely manner for inspection, analyze the cause, and carry out maintenance.
Temperature inspection: During operation, pay attention to the temperature changes of various parts of the gearbox, and the bearing temperature should generally not exceed 40 ℃. If the temperature is found to be too high, check whether the lubrication is normal, whether the load is too large, and whether the heat dissipation conditions are good.
Electrical system inspection: Check the power supply and wires of the reducer to ensure good connection, no damage, aging, or other phenomena. If there are any problems, they should be repaired or replaced in a timely manner to prevent electrical faults from causing safety accidents.
Gear and bearing inspection: Regularly open the gearbox cover to check the meshing condition of the gears, including meshing area, tooth side clearance, etc. Observe whether there is wear, deformation, annealing, spots, peeling and other phenomena on the surface of the gear teeth. At the same time, check the wear of the bearings and measure the axial and radial clearances. If severe bearing wear is found, it should be replaced in a timely manner.