How to conduct the debugging of a completed horizontal BWD10-13-1.1KW cycloidal pinwheel reducer
After the maintenance of the horizontal BWD10-13-1.1KW cycloidal pinwheel reducer is completed, the following steps can be followed for debugging:
Appearance inspection: Check whether the appearance of the reducer is damaged or deformed, whether the connecting parts are tightened, and whether the oil gauge, ventilator and other components are installed correctly and intact. Ensure that the surface of the reducer is clean, free of oil stains and debris.
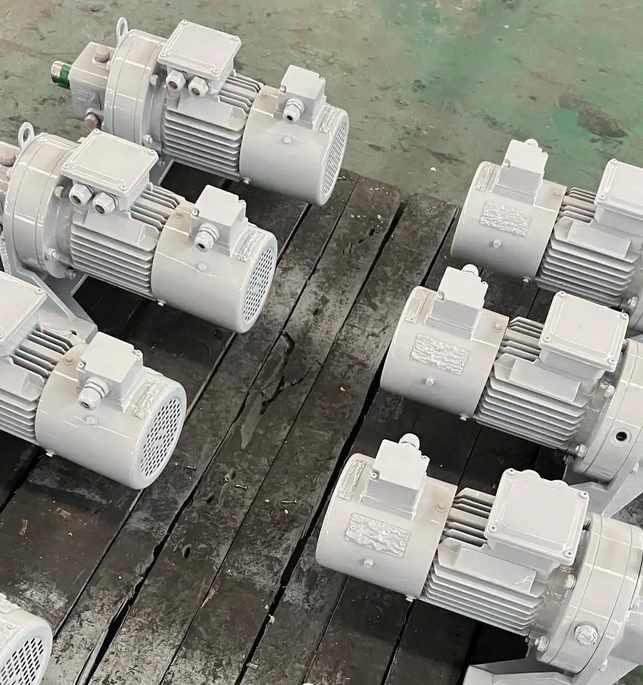
Manual turning: Before powering on, manually rotate the input or output shaft of the reducer to check for flexible rotation, any jamming, abnormal resistance, or collision. At the same time, observe whether there is any looseness or abnormal noise in each component.
Installation and connection inspection: Confirm that the reducer has been correctly installed on the equipment, whether the connection with the motor, working machine, etc. is accurate and correct, whether the installation of transmission devices such as couplings and pulleys meets the requirements, and whether the connecting bolts are tightened.
Lubrication system inspection: Check whether the oil level of the reducer is within the specified range and whether the oil quality is good. If the oil level is too low, lubricating oil that meets the requirements should be added; If the oil quality is poor, it needs to be replaced with new oil. At the same time, check whether the lubrication components such as the oil nozzle and oil pipe are unobstructed and whether there is any oil leakage.
Electrical connection inspection: For electric reducers, check whether the motor wiring is correct, whether the grounding is good, and whether the insulation resistance meets the requirements. Ensure that the electrical system is free from safety hazards such as leakage and short circuits.
No load debugging: Connect the power supply and let the gearbox run in an unloaded state for a period of time, usually 2-4 hours. Observe the operation status of the gearbox, including whether the motor starts normally, whether the gearbox operates smoothly, and whether there are any abnormal vibrations, heating, or other phenomena. Check the temperature rise of each component, especially key parts such as bearings and gears, and ensure that the temperature does not exceed the specified value. At the same time, check whether there is any oil leakage in the sealing part of the reducer.
Load debugging: After the no-load debugging is normal, gradually increase the load and perform load debugging. The increase in load should be carried out gradually, and can be loaded in stages to 25%, 50%, 75%, and 100% of the rated load. At each load stage, run for a period of time, observe the operation status of the gearbox, and check whether its torque, speed, temperature and other parameters are normal. Pay attention to whether there are any abnormal sounds, vibrations, or overheating during the loading process of the gearbox, and whether there is any looseness in the connecting parts. Check whether the operation of the working machine is stable and whether it is well coordinated with the reducer.
Precision adjustment: If the reducer is used in situations that require precise transmission, such as machine tools, automated production lines, etc., precision adjustment is also required. By measuring parameters such as output shaft speed and rotation angle, and comparing them with theoretical values, if there is a deviation, calibration can be performed by adjusting the motor speed, gearbox transmission ratio, or other related components.
Final inspection: After debugging is completed, stop the machine again to check all components of the gearbox, including whether the connecting bolts are loose, whether the lubricating oil needs to be replenished, and whether there is leakage in the sealing parts. Clean the oil and debris on the surface of the reducer, and do a good job in cleaning the equipment.