How to determine whether the durability verification test results of DCYK224-31.5-I gear reducer are qualified
To determine whether the durability verification test results of the gear reducer are qualified, the following standards can be used:
Gear wear condition: In a test of 2000 hours of full load operation, it is necessary to monitor the amount of tooth surface wear, which generally requires a small amount of wear. For example, after a 20000 hour acceleration life test of a planetary gearbox, the amount of tooth surface wear should usually be ≤ 15 μ m. If the wear exceeds the specified value, it will affect the transmission accuracy and service life of the gear and be considered as unqualified.
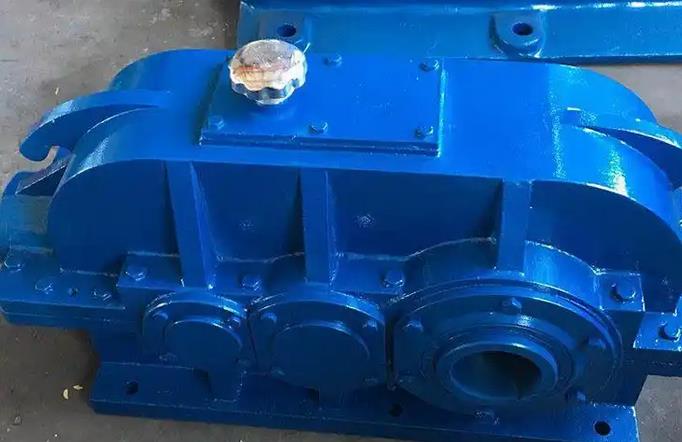
Gear contact spots: After simulating 50 start stop cycles per day and accumulating 5000 start stop cycles, check the gear contact spots. The contact spots should meet the requirements of gear meshing. If the distribution of contact spots is uneven or the area is too small, it indicates poor gear meshing, which will affect transmission efficiency and durability, and can be judged as unqualified.
Structural integrity: Apply a 150% rated torque impact load, repeat the overload impact test 100 times, and check the structural integrity of the gearbox. If there are situations such as gear breakage, bearing damage, or shell rupture, it indicates that the structural strength of the reducer is insufficient to withstand overload impact, and the test results are unqualified.
Efficiency attenuation rate: After durability testing, the efficiency of the gearbox will experience a certain degree of attenuation, but it is usually required that the efficiency attenuation rate be ≤ 3%. If the efficiency decays too much, it will lead to an increase in energy loss, a decrease in transmission performance, and not meet durability requirements.
Vibration and noise: During operation, the effective value of vibration velocity should comply with ISO10816-3 standard, and the sound pressure level under no-load/load conditions should generally be ≤ 65dB (A). If the vibration and noise are too high, it indicates that the gearbox is not running smoothly, and there may be problems such as poor gear meshing and bearing failure, which affect its durability and performance, and can be judged as unqualified.
Temperature situation: After continuous operation for a certain period of time, the temperature rise of the bearing position should generally be ≤ 35K, and the oil temperature is usually ≤ 95 ℃. If the temperature is too high, it will cause a decrease in the performance of the lubricating oil, exacerbate component wear, affect the normal operation and service life of the gearbox, and the test results will be unqualified.
Stress wave and abrasive particle monitoring: The stress wave sensor captures the stress wave during the gear meshing process. If the stress wave is abnormal, it indicates that there may be a potential fault in the gear. Regularly extract lubricating oil samples and use an iron spectrometer to detect the morphology and size distribution of abrasive particles. When layered abrasive particles>15 μ m are found, it indicates that the gear has entered an abnormal wear stage, which may affect the durability of the gearbox and require further evaluation to determine if it is qualified.