How to determine if the installation of DCYK400-63-1N hard tooth reducer is correct
To determine whether the DCYK400-63-1N hard tooth reducer is installed correctly, the following aspects can be taken into account:
Installation foundation and fixing inspection: The reducer should be firmly installed on a stable foundation or base. Check if the installation foundation is flat, sturdy, and free from looseness or vibration. If the foundation is unreliable, vibration and noise will be generated during operation, and in severe cases, bearings and gears may be damaged. At the same time, confirm whether all the fastening bolts of the reducer are tightened, and the tightening force of the bolts should be uniform to avoid loosening or over tightening.
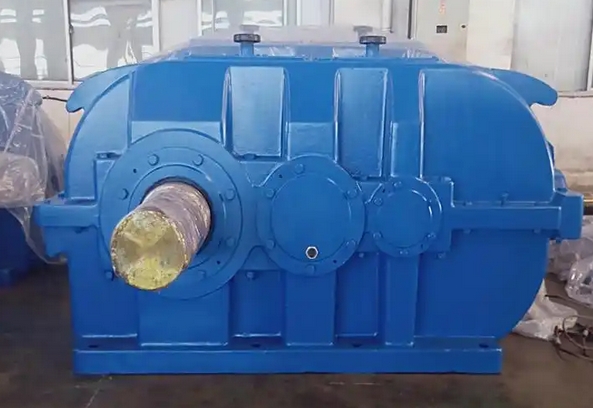
Connection component inspection: Check whether the connection between the input shaft and the power source (such as the motor), and the output shaft and the working machine (such as the conveyor belt, mixer, etc.) is firm. When connecting, it should be ensured that the concentricity between the input hole of the reducer and the input shaft of the motor is consistent, and the outer flanges of the two are parallel. For coupling connections, it is necessary to check whether the installation of the coupling is correct, and the error should not exceed the compensation amount of the coupling used. In addition, when installing transmission components on the output shaft, it is not allowed to strike with a hammer to avoid damaging internal parts.
Gear installation inspection: For hard tooth surface gear reducers, specific gear installation methods can be used to determine. For example, when one of the gears is rotated 180 degrees and the middle bearing hole and the ten holes are completely aligned, the outer tooth profile should be exactly misaligned, and the tooth heel position of the upper plate should be exactly the tooth tip position of the lower plate. Place a piece of gear into the needle gear housing and rotate it by hand to see if it flows smoothly and if there is any oscillation. Insert the eccentric bearing and ensure that the bearing hole of the lower gear completely accommodates the cylindrical ball of the eccentric bearing. Insert another gear accurately, then put on the shaft sleeve and rotate it to see if it is flexible.
Lubrication system inspection: After installation, the oil level should be thoroughly checked in sequence. According to different installation positions, open the oil level plug screw and check the height of the oil level line. The lubricating oil should be within the normal range. At the same time, confirm whether the type of lubricating oil meets the requirements. When refueling, ensure that the lubricating oil overflows from the screw hole of the oil level plug, and then tighten the oil level plug.
Sealing performance inspection: Check whether the sealing components on the gearbox housing are installed correctly, ensuring that the interior of the gearbox is not invaded by external impurities and liquids, and there is no oil leakage. Attention should be paid to the direction and sealing performance of the oil seals installed on the shaft heads of the input and output shafts to prevent lubricant leakage.
Trial operation inspection: After installation, conduct a no-load trial operation for no less than 2 hours. During operation, check whether the reducer rotates flexibly and whether there is any jamming phenomenon. At the same time, observe whether the operation is smooth, whether there are any abnormal noises, impacts, vibrations, and oil leaks. If there are any abnormalities, stop the machine in time for inspection.